Generally speaking, self-lubricating bearings can be used for many years or tens of thousands of hours, depending on factors such as the bearing type, working environment, and workload. During the production process, it is necessary to regularly check the working condition of the self-lubricating bearing. If the following situations occur, you can consider replacing the self-lubricating bearing:
- Sound and vibration: Abnormal sounds, such as sharp friction sounds, humming sounds, or a significant increase in vibration, may indicate that the bearing is worn or damaged. You can use a sound meter to check the rolling sound of the bearing in operation. Abnormal sounds and irregular sounds may indicate bearing damage.
- Temperature and lubrication: If the temperature rises abnormally or the lubrication condition is poor, such as the grease turning black or drying, the bearing may need to be replaced.
- Appearance inspection: Manually rotate the outer ring of the bearing to feel whether it can rotate flexibly without radial shaking. Check the inner and outer raceways, rolling elements, and cages of the bearing to confirm that there are no cracks, peeling, severe wear, looseness, etc. If there is obvious wear, cracks, peeling, or deformation on the surface of the bearing, consider replacing it.
- Performance evaluation: If the equipment's operating efficiency is reduced or unstable, such as axial and radial displacement, it may be a bearing problem. The clearance between the inner and outer rings of the bearing and the rolling element can be measured, which should normally be 0.005~0.010mm, and the axial vibration should be performed without obvious sound.
- Maintenance records and life: Evaluate whether the bearing needs to be replaced based on its rated life, operating conditions and maintenance records.
In addition, the lubricating grease should be cleaned and replaced regularly, overload should be avoided, the working conditions of the bearing should be paid attention to, and the appropriate bearing should be selected to extend its service life. If any abnormal signs are found, further inspection should be carried out in a timely manner and necessary maintenance or replacement measures should be taken.
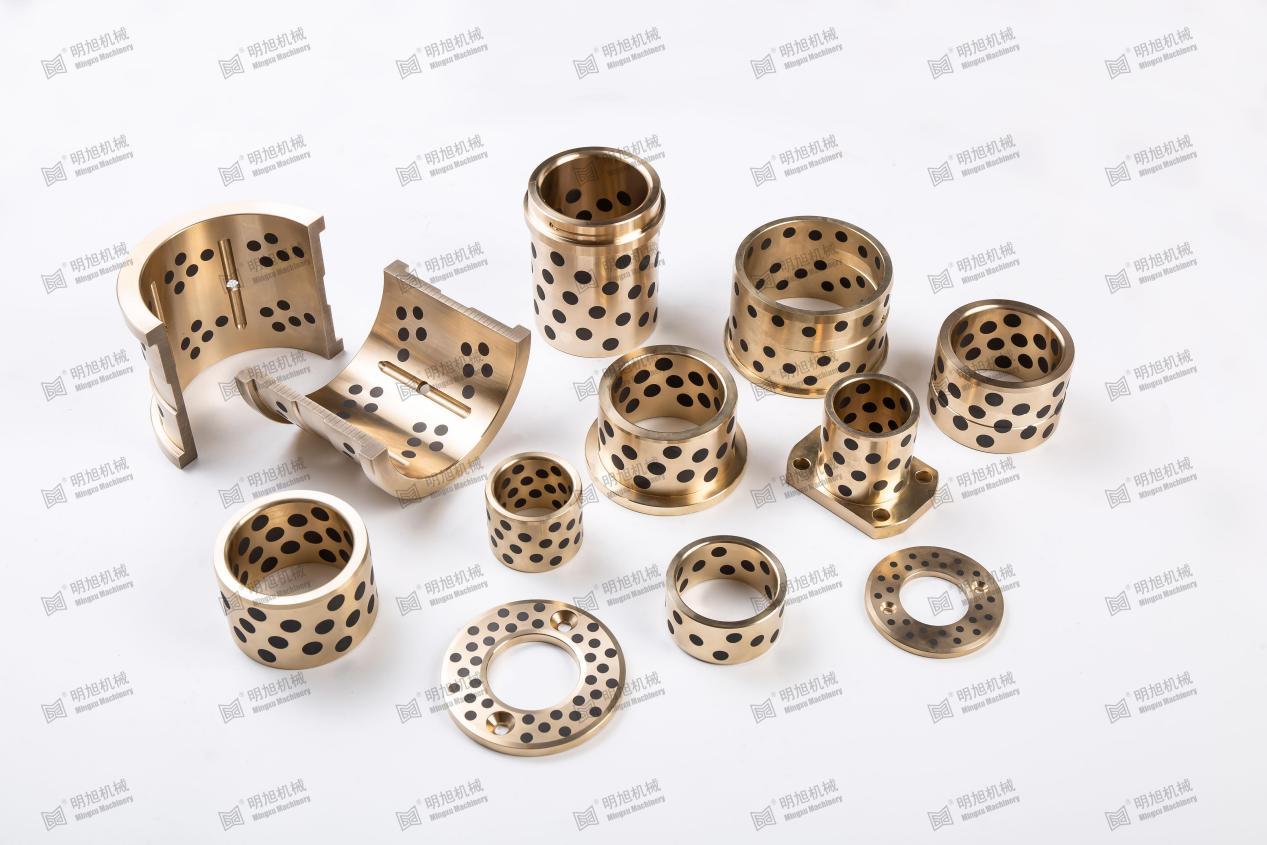
So, what should be paid attention to when choosing self-lubricating bearings?
- Understand the needs: Clarify the operating conditions and requirements of the mechanical equipment, including load, speed, temperature, etc.
- Choose the right type: Choose the right type of self-lubricating bearing according to the needs of the mechanical equipment.
- Consider the bearing life: According to the rated life and operating conditions of the bearing, reasonably evaluate the replacement cycle of the bearing. Consult an expert: During the selection process, you can contact Mingxu Machinery's sales staff at [email protected] at any time to ensure the accuracy and rationality of the selection.
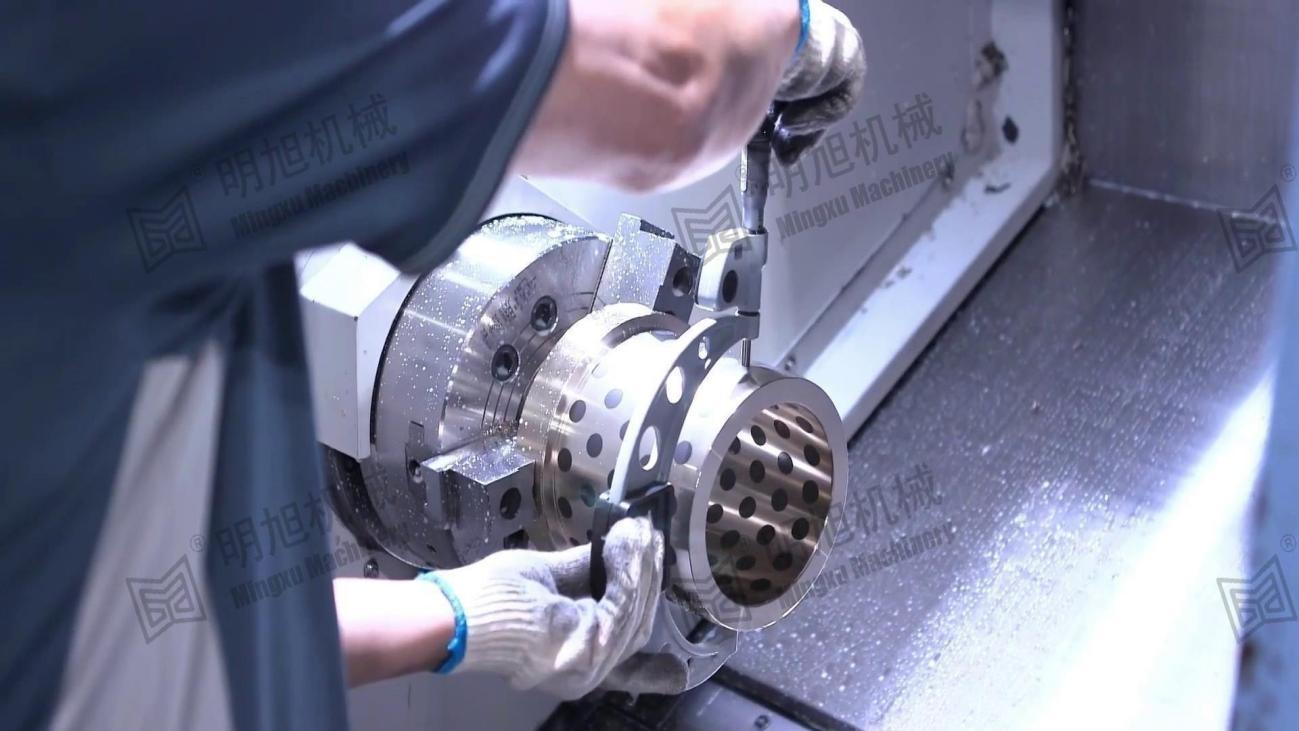
Matters needing attention when replacing self-lubricating bearings
- Preparation before installation: Clean the installation surface, remove impurities and oil stains; distinguish between the friction surface and the installation surface.
- Correct installation: Use the correct installation tools and methods to ensure that the bearing is installed in place and without eccentricity; fasteners need to be glued and loosened.
- Avoid damage: During installation and disassembly, avoid excessive force to prevent mechanical damage to the bearing.
Prevent pollution: Keep the working environment of the bearing clean to prevent foreign matter from entering the bearing.
Связаться с нами